From week one, we had two design constraints that we wanted to adhere to this season. The first was to get five power cells in a cycle. Predicting there would be a lot of congestion getting across the field, we felt it was vital to have all 5 power cells when each cycle. The second constraint was to keep the robot small. Not only does this have the advantage of fitting under the trench, but it would also make shipping a lot easier, as the robot will need to be disassembled into fewer pieces to ship on the plane. This created a lot of issues with fitting a power cell storage mechanism, but we found what we think to be a very creative solution.
On the second day of the season, Lawton created a CAD model of a basic circular mechanism which would fit five power cells, and could rotate to fit underneath the trench. He referred to it as “The Cheeto” because it had the shape of a Cheeto. While proposing it to the team, Josh came up with the idea to make it more circular, so the entire mechanism would fit without needing to tip back. This was first met with skepticism that 5 balls could fit in it while still being under, but after messing around with the CAD model, we determined it was possible.
After more deliberation, we came up with a design that would use 8 “prongs” to store the ball, and a center pivot point for rotating up to fire. It would have two wheels power by 775s to launch the ball, as well as feed balls into the Cheeto. An arm would rotate around eject the balls. We laser cut the first concept out of wood, assembled it, and tested. We immediately noticed two issues. First, the inside diameter (which was 7.1″ on the CAD model) wasn’t sufficient to hold the balls loosely. The second issue is the area where the shooter would attach was unsupported, so it would flex and potentially break when a ball entered.
With this in mind, we made the second prototype. This had a 7.5″ inside diameter, and had supports for the shooter. We tested intaking and shooting balls, but found more issues. The most critical was the intake mechanism. The flywheels didn’t have enough torque or grip to move the power cells up the Cheeto, only allowing us to store three before jamming. It also wasn’t able to be assembled from one piece, as each prong on the Cheeto had to bend too far to set into the ring holding them. We changed the arm that ejected the ball to a wheel which would both intake and eject, which required cutting only one hole in the current prototype. This worked much better, however we would need to modify how it grips the ball to ensure there weren’t points too tight or too loose. We also changed how the pieces attached from friction to rivets to ensure it could be assembled from a continue prong when we fabricate the metal version.
This last week, with this prototype working, we sent finished drawings to General Mechanical to fabricate. We hope to receive the components for the metal version Monday, and assemble and mount it to our robot. We are very impressed with the mechanism, and hope it serves us well in competition this season.
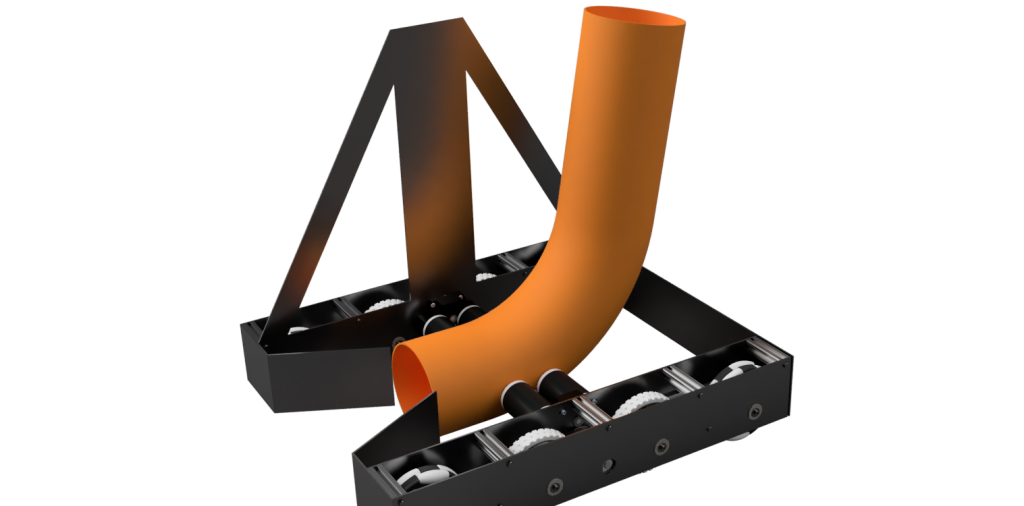
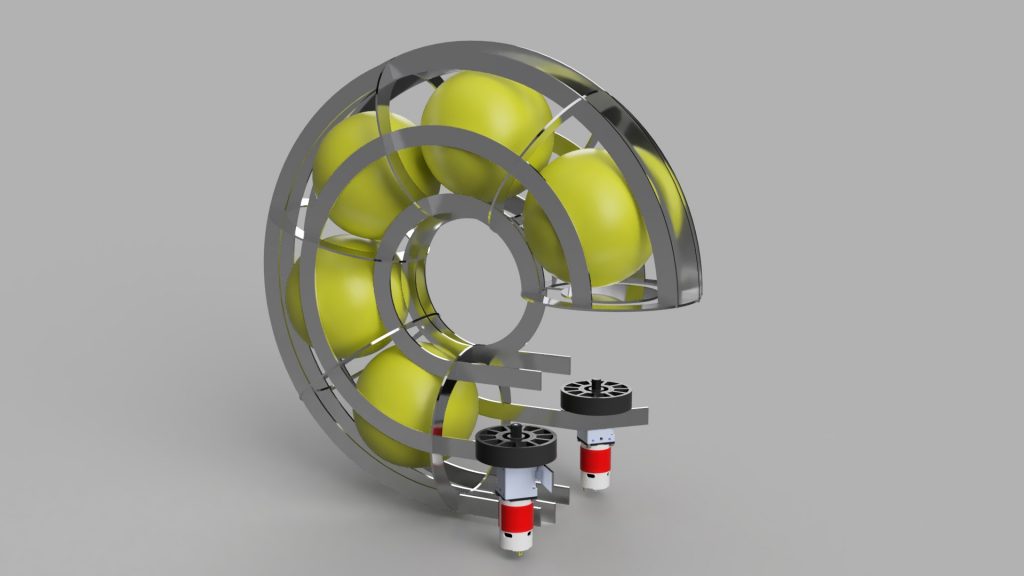
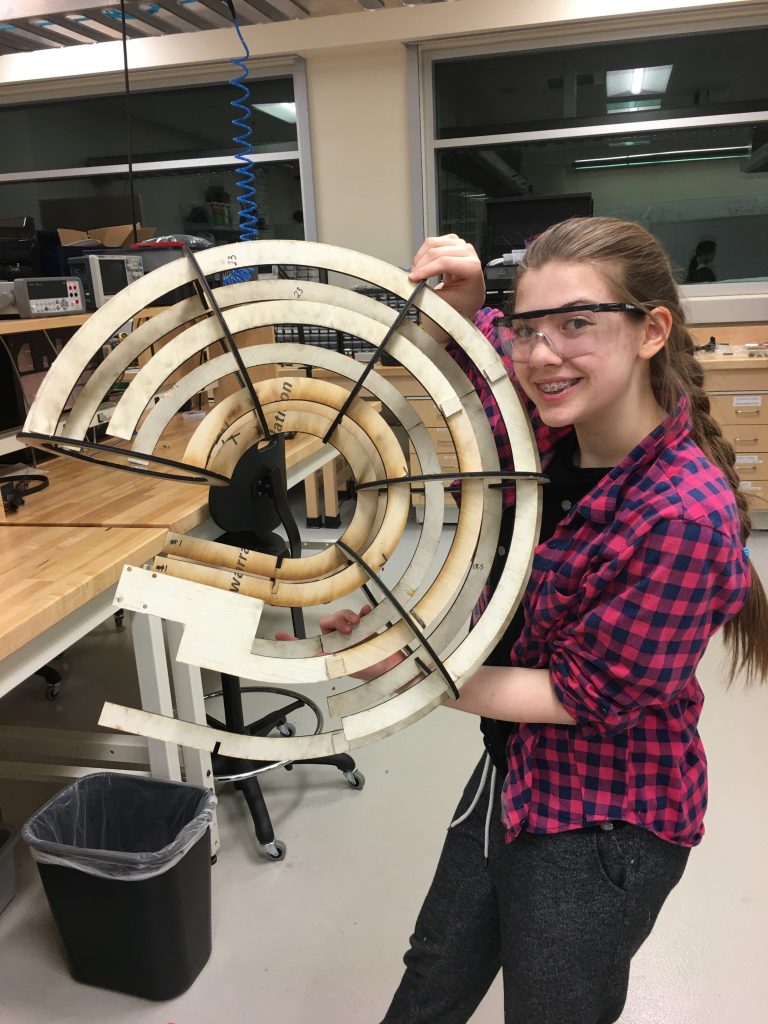