With another year comes another season, and while this year’s challenge is considerably different than anything our team has done before, we’re excited to see what this season holds! Among the other challenges we’re participating in, we will be competing in the robot design challenge. And while we’d love to have a normal season if things were able to return to normal, we think this gives us an exciting opportunity to learn from the past season and improve upon our design.
For the first week or two, we had a big question to solve: do we design from scratch, or modify our existing robot? We jumped back and fourth, coming up with ideas to improve the existing bot and concepts for a new bot, and decided to do both. We won’t be able to meet in person this season (except for when competing), but nevertheless, we’ve found ways to still build not one, but two robots.
The first step was CAD. While our team has traditionally created CAD models of robots before we jumped in, this season we were much more invested. We made some tweaks to last year’s robot to update it to its current form, and began looking at ways to modify it. We knew the intake would need major changes if it were to stay, but looking to take advantage of the larger role of the human player this year, we decided to remove it. However, that would mean the Cheeto needs some extensive modifications to intake a ball from the human player. Toya took lead on that, designing a large hopper that would fit onto the Cheeto and hold 3 balls the human player would drop in.
Meanwhile, work also began on a new shooter design. Lawton created the original concept, which took advantage of the taller robot configuration to have a shooter above storage for three power cells. The original design had the body of the shooter tip back to load power cells, however we later decided to increase the height slightly to have a rear hatch that can open, preventing the need for pneumatics and a tall support structure. For the drivebase, we stuck with our tried and true drivebase design of having 8 wheels, the middle four of which are dropped slightly and powered, and the outer four for stability. This year we also went with a wood design supported by aluminum angle for ease of fabrication, and decided to try only two falcon motors for the drivetrain. This was mostly due to a lack of Falcon motors, however also because the entire robot is considerably smaller and lighter than previous designs, so two may be sufficient for our needs.
With the design complete, prototyping began. The first shooter prototype was made with laser cut wood, and powered by two CIM motors. Loading was quite difficult, requiring a ball to first be placed inside, and the pushed up to contact the flywheel. In our tests, this looked to be considerably more powerful than last year’s shooter, validating our concept and progressing to a new prototype.
Our second prototype was the familiar shooter mechanism, however attached to a long base to load and shoot three balls. The shooter continued to work well, however we discovered issues with the loading mechanism. As the balls would travel up the magazine, they would contact the wood and get stuck along the side. This was compounded when multiple balls were loaded, making it nearly impossible to load three balls. Marcus, one of our mentors, suggested we coat the wood in wax, which he lent to us to try. This significantly reduced the problem, further validating this concept.
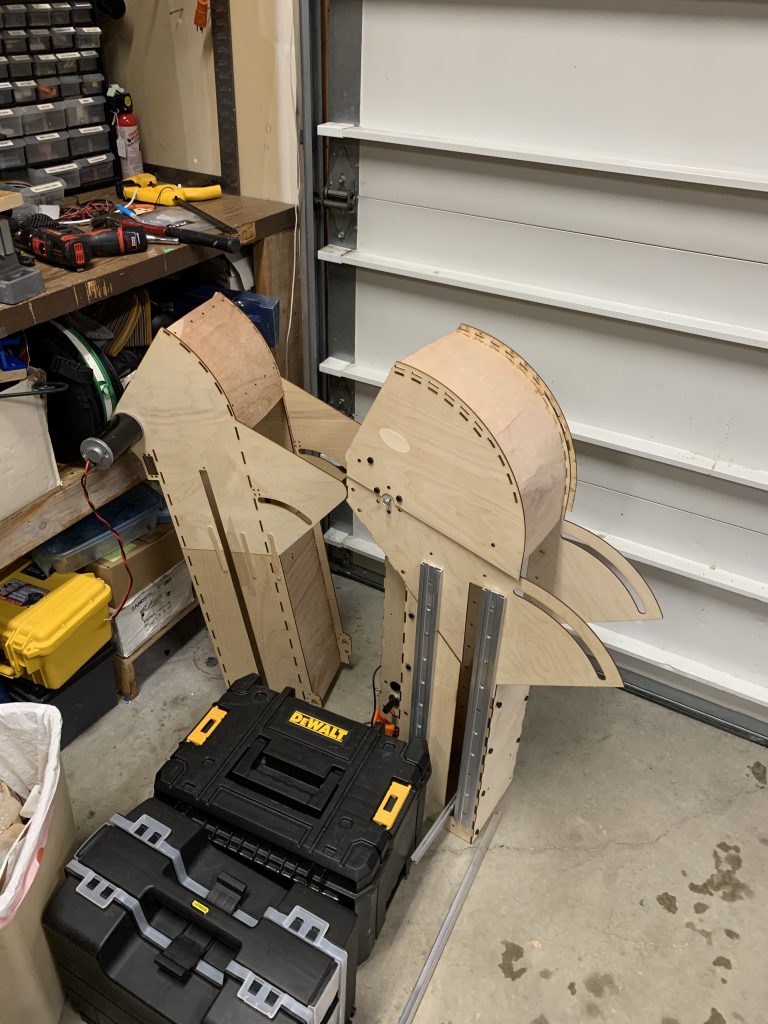
On our third prototype we continued to iterate on what we learned in the first two. The major change to this prototype was the addition of the Falcon motors instead of the CIMs. We also added rails for the feeding mechanism, a mount for a hood, and a slightly thinner magazine. It was also the first design to be supported by aluminum angle instead of glue. Our first discovery is the belt was in need of tensioning, as at full speed it was moving nearly 60 mph, and whipping around a ton. We added a small ball bearing tensioner, which improved the belt. It continued to shoot like the previous ones, however when we measured the distanced, we discovered it was considerably less than the math would suggest. After measuring the actual speed of the flywheel, the ball was expected to shoot at nearly 50 mph, however ended up shooting just over 20. To fix this, we’re now working on a test which will change 5 variables to determine how to best transfer power to the ball, including compression, wheel type, and shooter mass.
In these coming weeks, we hope to assemble and integrate the shooter with the drivebase, get some practice going, and decide which robot design we’ll use to compete with this year.